Self tapping socket head screws have become an essential component in various industries, known for their ability to create their own threads as they are driven into materials. This capability not only facilitates secure fastenings without pre-drilling but also enhances efficiency and productivity in manufacturing and assembly processes. These screws are distinguished by their socket head design, which allows for greater torque and precision during installation.
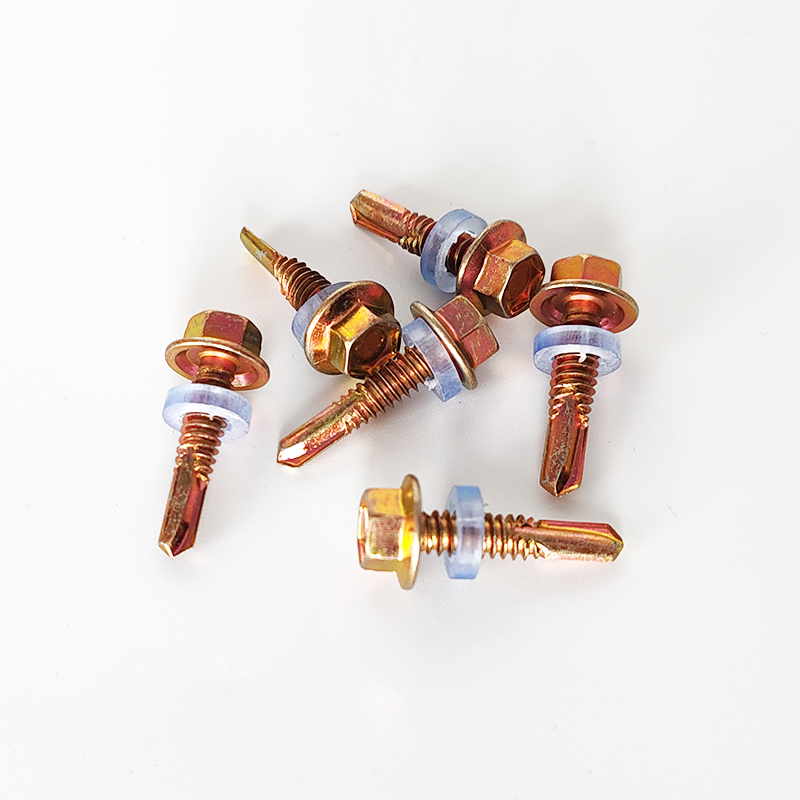
From an experience standpoint, self tapping socket head screws offer unmatched convenience, particularly in applications where speed and ease of use are crucial. Users report that these screws significantly reduce the time required for assembly tasks, as there’s no need for pre-drilled pilot holes. This feature is especially beneficial in high-volume production environments where time is of the essence and consistent results are mandatory.
In terms of expertise, understanding the precise applications and material compatibility is crucial for leveraging the full potential of these screws. Typically, self tapping socket head screws are made from high-quality materials like stainless steel, carbon steel, or alloy steel, ensuring they can withstand various environmental conditions. Their design features a hexagonal recess, allowing for the application of high torque without damaging the screw head, thus ensuring a stable and durable connection. Engineers and technicians within industries such as automotive, electronics, and construction often prefer these screws due to their versatility and reliability.
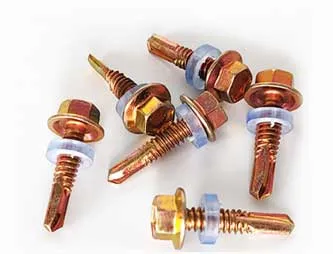
Authoritativeness comes from the extensive research and innovations that back the design of self tapping socket head screws. Top manufacturers often invest in R&D to produce screws that meet rigorous industry standards. They conduct comprehensive testing to ensure these screws can perform under high stress and in demanding environments. Publications in industry journals and case studies from leading companies serve as evidence of the trust and dependency placed on these components.
self tapping socket head screws
Trustworthiness in self tapping socket head screws is obtained through compliance with international standards such as ISO and ASTM. This ensures consistency in quality and performance across different batches and manufacturers. Users can rely on these screws for critical applications as they offer a secure fastening solution while minimizing the risk of over-tightening and material damage. Furthermore, many manufacturers provide certification and quality assurance processes, adding another layer of reliability.
A notable advantage of self tapping socket head screws is their adaptability across different materials, including metals, wood, and some plastics. This adaptability stems from the engineering behind their threading design, which not only cuts but also forms threads in the substrate.
Selecting the right size and type of screw is paramount. For instance, screws with coarse threads are ideal for softer materials, while fine threads are better suited for harder materials, ensuring optimal penetration and grip.
In summary, self tapping socket head screws blend engineering precision with practical efficiency. Their unique design and the material quality provide users with a dependable fastening solution that suits various applications. By choosing self tapping socket head screws, industries can achieve a balance of performance, reliability, and ease of use. From automotive to construction, these screws remain a staple due to their ability to simplify installation processes and ensure long-term fastening integrity, demonstrating their indispensable role across sectors.