When dealing with precision engineering projects, finding the right fasteners is crucial for both stability and longevity. The 3/8-24 double-ended stud delivers an unparalleled solution for professionals who require dependable and versatile components. This article delves into the unique properties and applications of this essential tool, providing authoritative insights and trustworthy guidance for its selection and use.
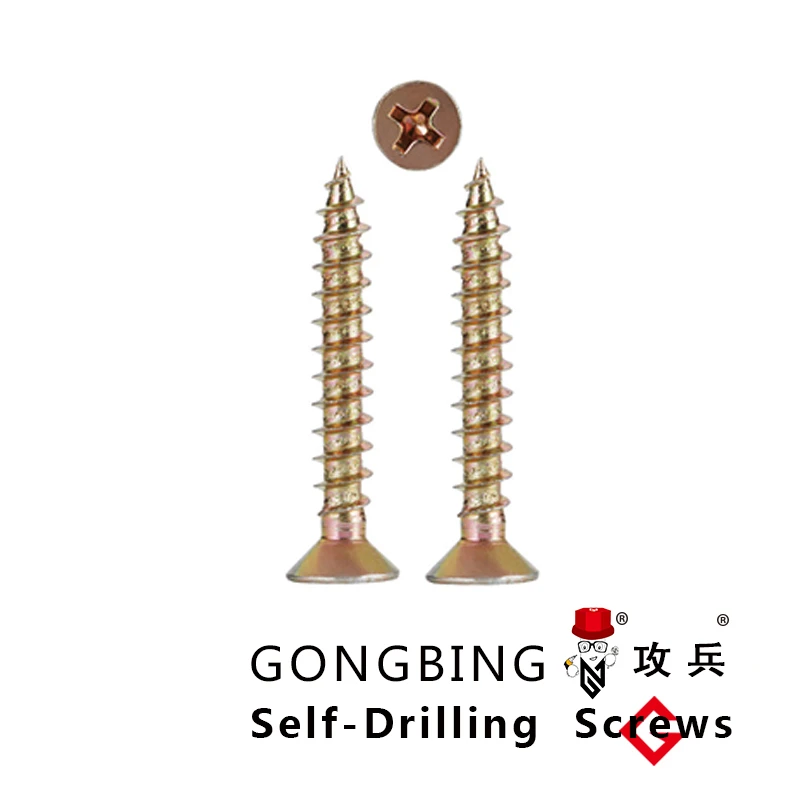
A double-ended stud, also known as a double-threaded bolt or stud bolt, is characterized by its threaded rods on both ends. Its design allows for components to be fastened securely between two nuts, or into one nut and another receiving material. The 3/8-24 double-ended stud, named for its diameter and thread pitch, is particularly favored in applications that demand high precision and reliability.
Understanding the specifications of 3/8-24 is fundamental to appreciating its applications. The 3/8 represents the nominal diameter of the stud, making it a reliable choice for moderate load-bearing applications. The 24 indicates the number of threads per inch, which ensures a fine-threaded stud providing greater tensile strength and more controlled tightening adjustments compared to coarse-thread studs. As experts know, fine threads are particularly advantageous in situations where vibration might cause a fastener to loosen.
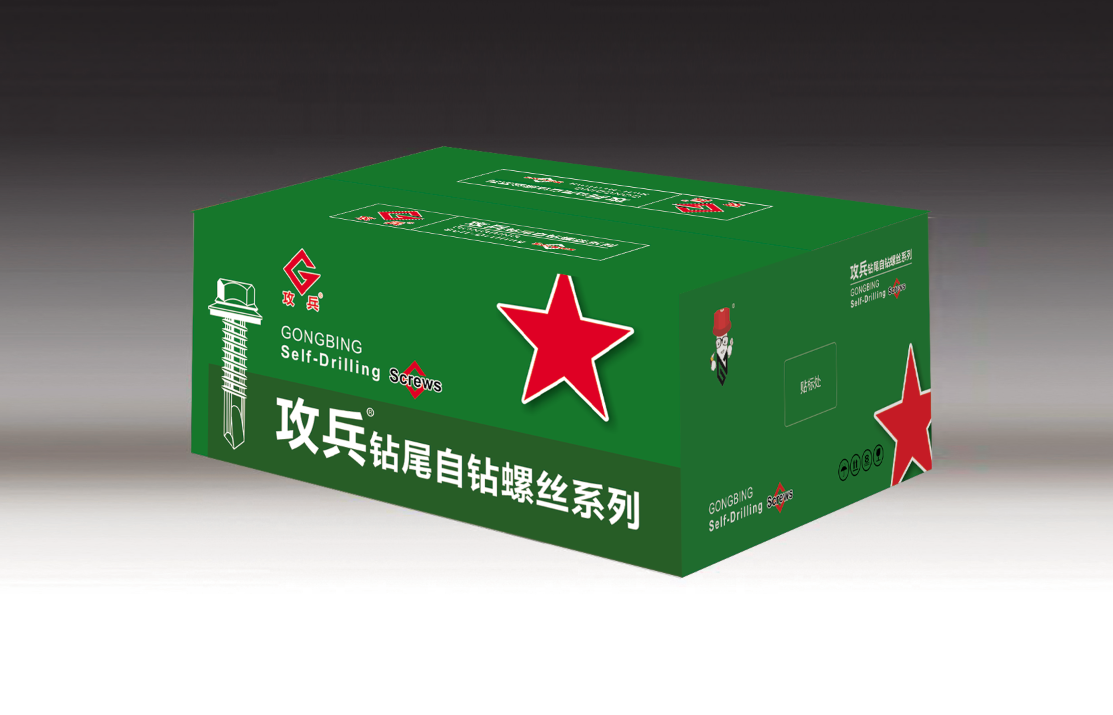
The expertise required to select the correct stud involves understanding the material properties it offers. Double-ended studs made from stainless steel are prevalent due to their resistance to corrosion, maintaining integrity even in harsh environments. This makes them suitable for sectors like automotive, aerospace, and marine industries where exposure to moisture and chemicals is routine. Alternatively, for projects where weight is a concern, titanium variants provide a robust yet lighter option.
An application where the 3/8-24 double-ended stud stands out is in automotive engine assembly. Here, accurate torque application is vital. The fine-thread profile aids in achieving precise tensioning, which is essential when attaching engine components such as cylinder heads. This precision assures continued performance, affirming trust in the component's reliability during high-speed operation.
3 8 24 double ended stud
Installation expertise is a crucial aspect that cannot be overlooked. When fitting a 3/8-24 double-ended stud, utilizing a torque wrench is mandatory to ensure that exact specifications are met, preventing over-tightening which could lead to stripping. Equally, the thread needs to be clean and burr-free for proper fitment, supporting consistent application of pressure across the surface area of the fastening.
Experts recommend considering additional treatments such as zinc plating for environments where additional corrosion resistance is needed without compromising the stud's integrity. This allows for extended use in unfavorable conditions, further extending the reliability and lifetime of the application.
Building trust in this component comes from its verifiable usage in high-stakes industries. From race car assembly lines to cutting-edge aerospace projects, the 3/8-24 double-ended stud is synonymous with reliability and precision. Its adoption by engineers around the globe is a testament to its authoritative position in the world of fasteners.
Finding trustworthy suppliers is another crucial step to ensure the authenticity and quality of these studs. Professional recommendation points towards vetting suppliers for ISO certifications and ensuring that they provide material test reports, guaranteeing that the studs meet industry standards and are manufactured to precise specifications.
With this comprehensive exploration, utilizing the 3/8-24 double-ended stud in your projects promises enhanced performance and reliability. The technical prowess allied with steadfast supplier and installation practices assures that your engineering endeavors will benefit from one of the market's most dependable fastening solutions. Embrace the potential of this tool to elevate the precision and security of your structural assemblies, knowing that it steadfastly balances innovation with foundational engineering principles.