Navigating the complex world of industrial components can be daunting, yet understanding the nuances of A325 fasteners ensures that projects meet their structural integrity requirements while maximizing safety. As a seasoned expert in the field of industrial fasteners, the knowledge shared here stems from real-world applications, authoritative research, and extensive industry expertise.
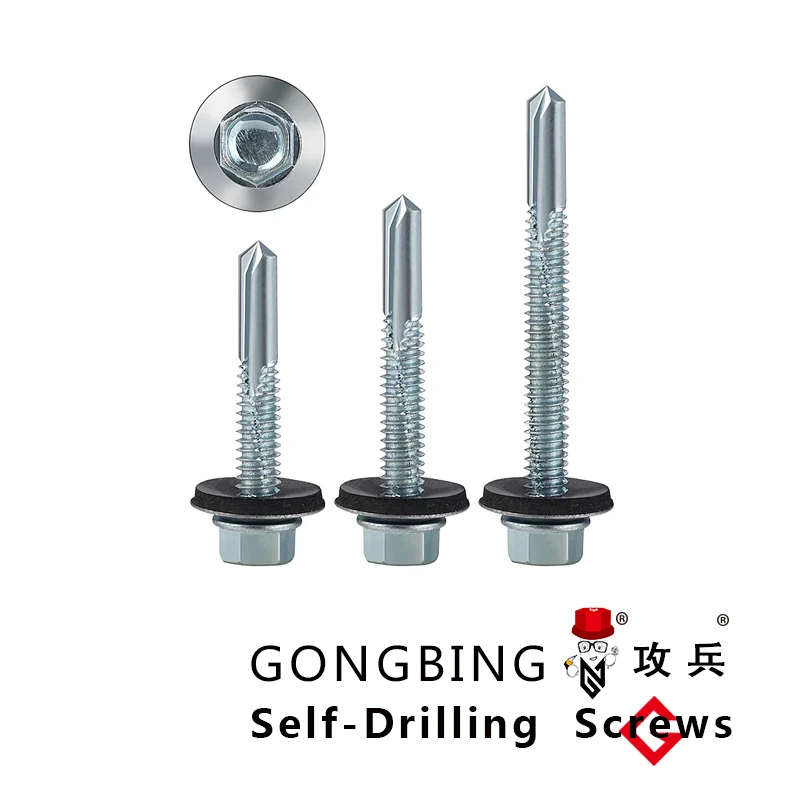
A325 fasteners, commonly found in high-strength structural connections, are integral to various construction projects due to their ability to withstand significant tension forces. These bolts are particularly prevalent in steel-to-steel connections, underpinning infrastructure projects such as bridges, buildings, and heavy machinery. Their specific design ensures optimal performance under stress, making them a go-to choice for engineers and builders worldwide.
In practice, these fasteners are characterized by certain material and dimensional properties that differentiate them from regular bolts. Made from medium carbon steel, they are designed to fulfill stringent tensile strength and hardness criteria, ensuring that two steel plates can be securely joined without the risk of deforming the fastener. They've been designed to meet ASTM specifications, which outline their size, shape, load-bearing capacity, and the manufacturing processes necessary to achieve these standards.
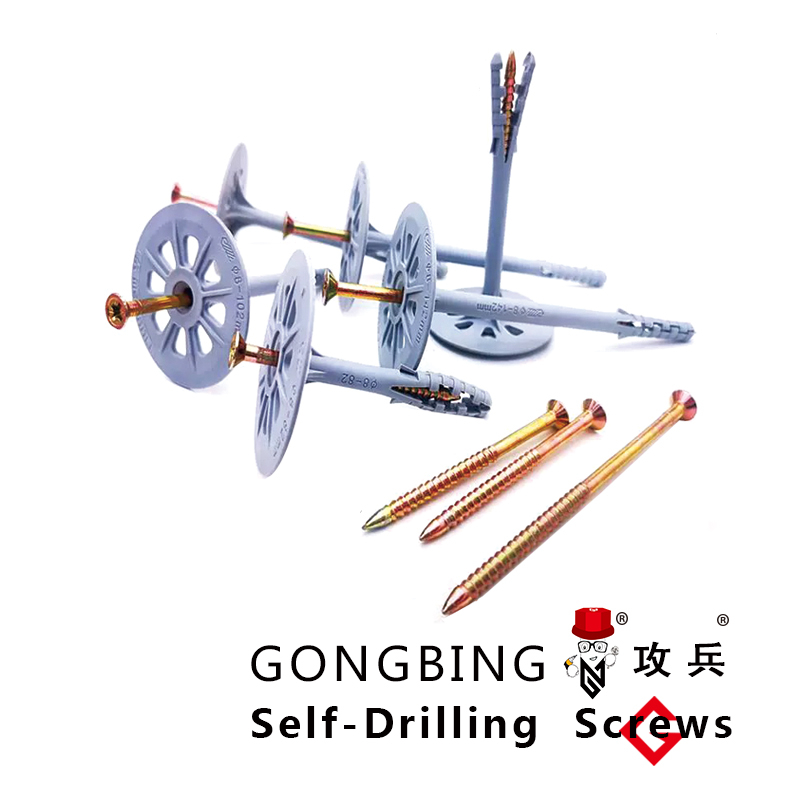
An essential aspect to understand when using A325 fasteners is their classification into two types Type 1 and Type 3. Type 1 is plain carbon steel, commonly used for general applications. In contrast, Type 3, which contains a weathering steel composition, provides enhanced atmospheric corrosion resistance, especially useful in outdoor installations without additional protective coatings. Utilizing the correct type for the environment not only extends the lifespan of the structure but also ensures compliance with industry regulations.
Installation of A325 bolts requires precision and care. Fasteners should be installed using calibrated wrenches to apply the correct tension, ensuring that the joint uses both the friction of the clamped materials and the potential for bolt elongation under load to maintain stability. Professionals often employ the turn-of-nut method or a direct tension indicator to verify that each bolt achieves the proper preload, crucial for maintaining the structural integrity of heavy-load applications.
a325 fasteners
A325 fasteners are also pivotal in achieving seismic resilience in construction. Their ability to maintain performance during dynamic loading conditions, such as those experienced during earthquakes, is a testimony to their reliability and durability. Structures built with these fasteners are better equipped to withstand shifting and vibrations, thus safeguarding infrastructure and potentially saving lives.
Integration of A325 fasteners into a project necessitates a comprehensive understanding of the overall structural dynamics. Engineers and architects must collaborate efficiently, acknowledging the impacts of force distribution and material compatibility. Every joint in a constructed structure plays a critical role in its overall performance; thus, the use of A325 fasteners signifies a commitment to adopting best practices and adhering to standards that enhance both safety and efficacy.
Endorsed by industry standards and benefiting from decades of applied use, the expertise surrounding A325 fasteners is rooted in their proven track record. It's no wonder these fasteners are considered a critical component in the toolbox of professional engineers and builders aiming for excellence in construction.
Ultimately, A325 fasteners aren't just a component—they represent a commitment to enduring safety and engineering excellence. A project with these fasteners brings not only compliance with regulatory standards but also assurance, trust, and the promise of longevity and reliability in construction. This comprehensive understanding and apt application underscore A325 fasteners as pillars in the domain of modern structural engineering.