Aircraft Structural Fasteners Ensuring Safety in the Skies
Aircraft structural fasteners play a critical role in ensuring the safety and reliability of modern aircraft. These small but essential components are responsible for holding together various parts of the aircraft, including fuselage sections, wings, and tail structures. Given the extreme conditions that aircraft operate under, such as high speeds, varying temperatures, and intense vibrations, it is imperative that the fasteners used in the construction of aircraft are of the highest quality and reliability.
Aircraft structural fasteners come in various forms, including bolts, nuts, rivets, screws, and pins. Each type of fastener is designed to perform a specific function, whether it's providing a secure connection between two parts or allowing for easy disassembly and reassembly of components for maintenance and repairs. These fasteners are typically made from durable materials such as stainless steel, titanium, or aluminum, which are chosen for their strength, corrosion resistance, and lightweight properties.
One of the key considerations in the selection of aircraft structural fasteners is their compatibility with the materials they will be fastening together. For example, aluminum fasteners are often used in conjunction with aluminum components to prevent galvanic corrosion, while stainless steel fasteners are preferred for attaching steel parts due to their superior strength and resistance to rust.
In addition to material compatibility, the design and installation of aircraft structural fasteners are also critical factors in ensuring the integrity of the aircraft. Fasteners must be properly torqued to the manufacturer's specifications to ensure that they provide the necessary clamping force to hold parts together securely Fasteners must be properly torqued to the manufacturer's specifications to ensure that they provide the necessary clamping force to hold parts together securely
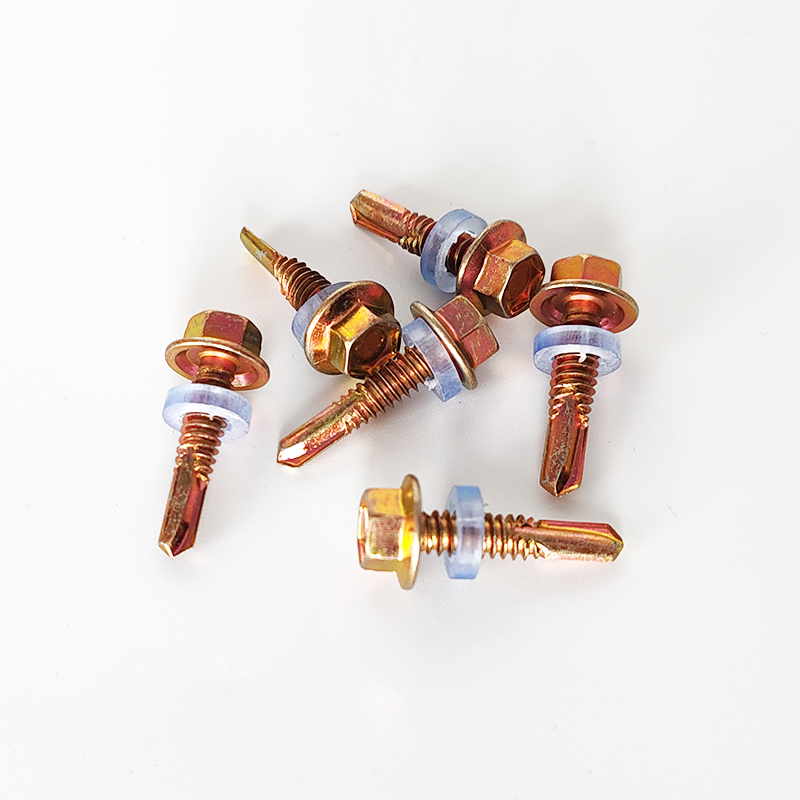
Fasteners must be properly torqued to the manufacturer's specifications to ensure that they provide the necessary clamping force to hold parts together securely Fasteners must be properly torqued to the manufacturer's specifications to ensure that they provide the necessary clamping force to hold parts together securely
aircraft structural fasteners. Improperly tightened fasteners can lead to structural failures, in-flight vibrations, and even catastrophic accidents.
Regular maintenance and inspections are essential to ensure that aircraft structural fasteners remain in optimal condition. Over time, fasteners can become worn, corroded, or damaged due to the stresses and strains of flight operations. Routine inspections can detect any signs of wear or damage, allowing for prompt replacement of fasteners before they pose a safety risk.
In conclusion, aircraft structural fasteners are a crucial component of aircraft construction that plays a vital role in ensuring the safety and reliability of commercial and military aircraft. Proper selection, installation, and maintenance of fasteners are essential to prevent structural failures and accidents in the skies. By adhering to strict quality control standards and regular maintenance procedures, aircraft manufacturers and operators can rest assured that their aircraft are held together by fasteners that meet the highest safety standards.