Resin anchors have revolutionized the way builders and engineers approach blockwork and masonry projects. Designed to deliver robust anchoring solutions where traditional methods may falter, resin anchors serve as a reliable choice for complex construction scenarios. They offer superior load-bearing capacity and enduring stability, ensuring structures remain secure and steadfast over time.
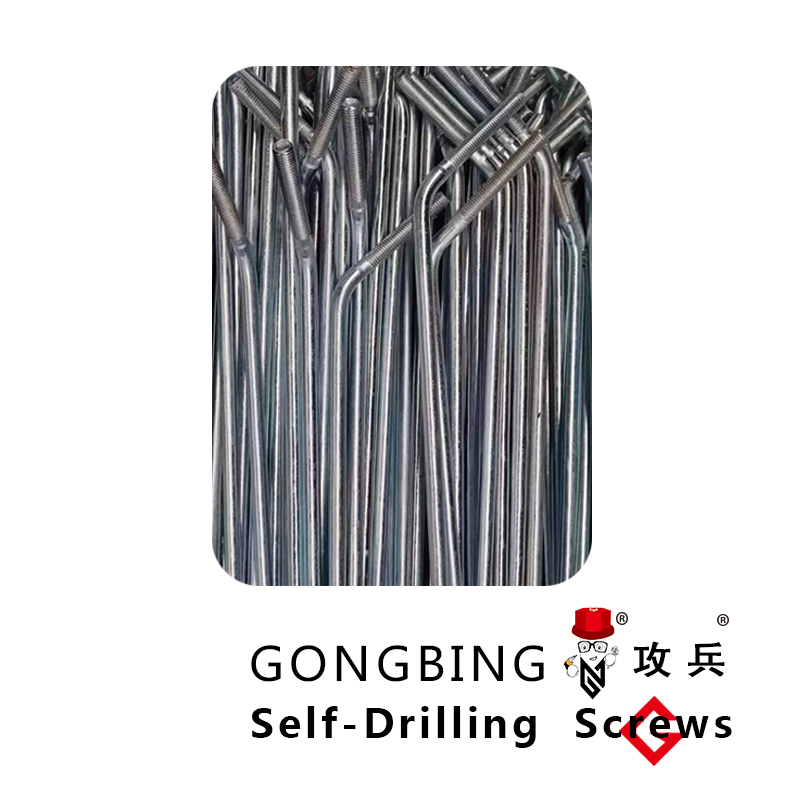
Resin anchors are particularly advantageous when working with blockwork due to their ability to bond and cure effectively in variable conditions. Their unparalleled adaptability means they can be used both in hollow and solid blocks, ensuring versatility across a wide spectrum of construction tasks. The ability to harden quickly without exerting expansive pressure reduces the risk of cracks or structural damage, a common concern with mechanical anchors.
One of the primary reasons resin anchors outperform their mechanical counterparts is their mechanism of load distribution. By bonding with the substrate material, resin anchors evenly distribute the load across the entire drilled area, reducing stress concentration points and enhancing the overall strength of the anchor system. This is crucial in blockwork constructions where the material may have inherent weaknesses such as air pockets or inconsistencies.
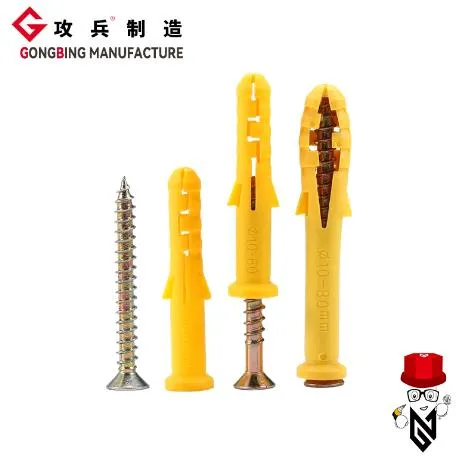
Expertise in the selection and application of the right type of resin anchor is essential. Epoxy-based resins are preferred when dealing with high-load scenarios due to their exceptional bonding strength and chemical resistance. Polyester resins, however, offer a more cost-effective option for lighter loads and less demanding conditions. Ensuring the correct mixture and thorough injection of resin is pivotal to achieving the desired performance, as incomplete applications can lead to suboptimal anchorage.
Professionals with extensive experience in masonry and blockwork recognize the importance of environmental conditions during the installation of resin anchors. Factors such as temperature, humidity, and the presence of moisture can significantly influence the curing process. Therefore, selecting resins with appropriate cure times and resistance to environmental influences is vital. For instance, fast-curing resins designed for cooler environments help maintain project timelines while ensuring reliability.
resin anchors for blockwork
Testing and certification of resin anchors further attest to their credibility in critical structural applications. Most high-quality resin systems undergo rigorous testing to meet international construction standards, such as ASTM or EN standards, providing peace of mind to engineers and project managers. This authoritative backing ensures that when resin anchors are employed, they will perform as specified under defined conditions, reinforcing their dependability.
Trustworthiness in resin anchor applications is built on more than just product performance; it relies heavily on installers’ skill and knowledge. Adequately trained professionals ensure that the preparation and application follow best practice guidelines, which is crucial in maximizing the anchors' effectiveness. This involves precise drilling techniques, appropriate hole cleaning, and ensuring the correct consistency and volume of resin is used.
Safety considerations also underscore the importance of resin anchors in blockwork. In seismic zones or areas subject to high winds, the enhanced grip provided by resin anchors can prevent catastrophic failures. Their use in overhead applications, such as ceiling mounts or suspended fixtures, highlights their reliability in scenarios where the safety and stability of structures are non-negotiable.
In conclusion,
resin anchors offer an indispensable solution for modern blockwork. Their superior strength, adaptability, and reliability make them a preferred choice for professionals seeking durable and long-lasting construction outcomes. With ongoing advancements in resin technology and installation techniques, the future of resin anchors in blockwork applications promises continued innovation and enhanced performance, ensuring they remain at the forefront of construction solutions.