Self tapping wafer screws have, over recent years, become indispensable in the realm of construction and manufacturing due to their unique capabilities and versatility. These innovative fasteners cater to diverse applications, from delicate electronic assemblies to robust construction projects, offering unmatched ease of use and precision.
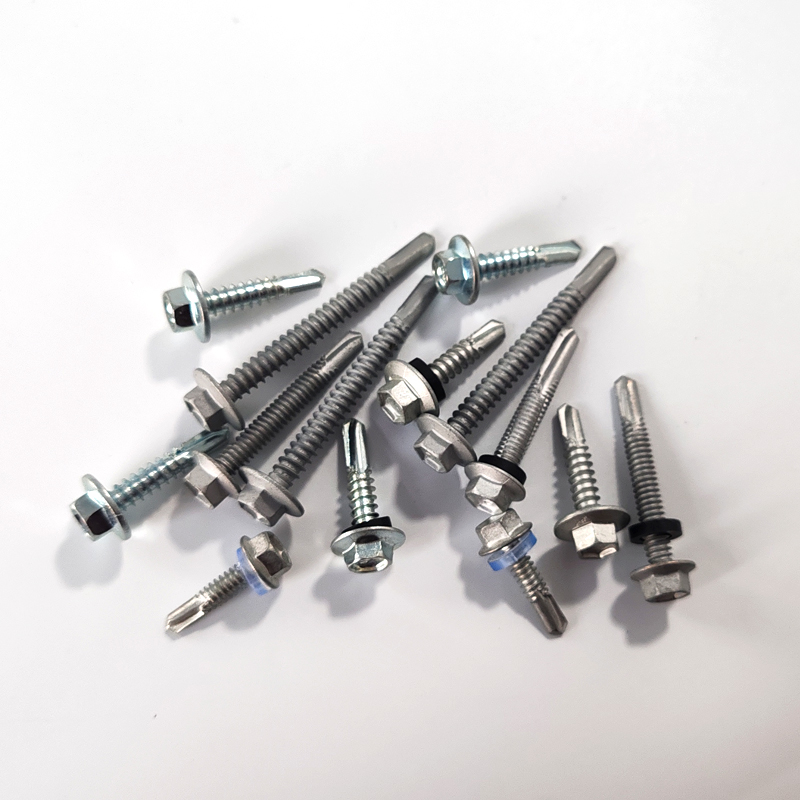
In terms of experience, countless professionals across industries have hailed these screws for their straightforward application process. Unlike traditional screws that require pre-drilled holes, self tapping wafer screws are engineered to tap their own threads as they are driven into the material, significantly reducing labor time and cost. Users from the automotive, aerospace, and electrical industries frequently report their efficiency in scenarios where time is of the essence and precision cannot be compromised.
From a perspective of expertise, understanding the design and function of self tapping wafer screws reveals their several intrinsic advantages. First, their wafer head profile—a broad, flat shape—ensures a large surface area, providing enhanced clamping force and better load distribution. This design is particularly beneficial in materials that might otherwise be at risk of cracking or damage under concentrated pressure, such as thin metals and plastics. The sharp, cutting threads are specifically crafted to pierce through these materials while creating a tight fit, thereby enhancing the structural integrity of the assembly.
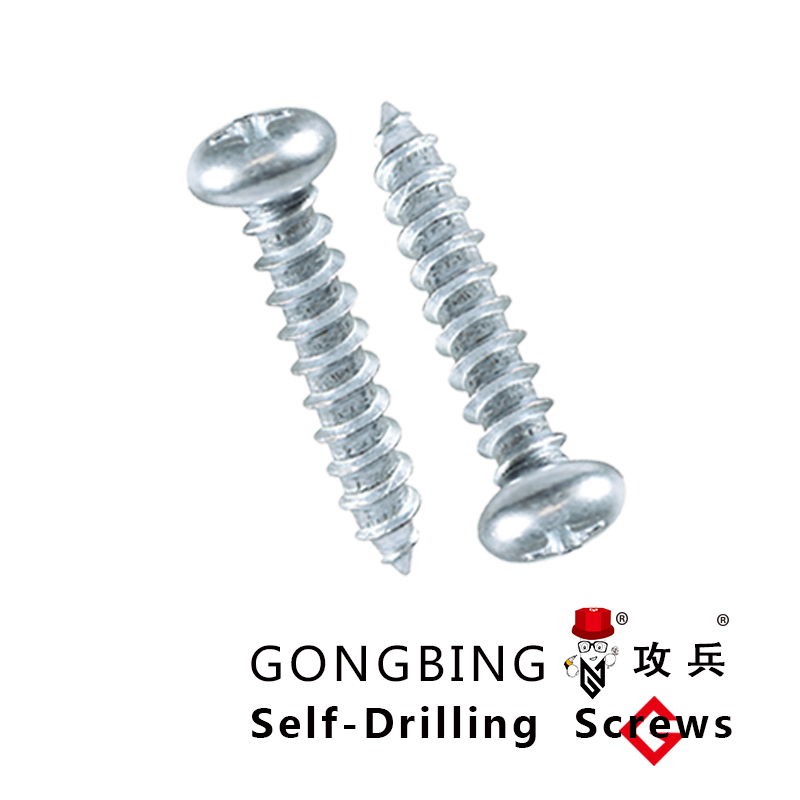
Moreover, the authoritative use of self tapping wafer screws is highlighted in various standards and guidelines set by industry leaders. The American National Standards Institute (ANSI) and the International Organization for Standardization (ISO) have both recognized the relevance of these screws, offering specifications that govern their manufacture and use. These regulations assure engineers and constructors of their reliability and consistency, which is paramount in fields demanding high precision and safety.
self tapping wafer screws
When considering trustworthiness, the performance history of self tapping wafer screws speaks volumes. Situations such as the construction of prefabricated construction units or assembling electronic enclosures demonstrate the screws' dependability. Testimonials from project managers and engineers consistently acknowledge not only the time savings but also the reduction in material waste. The pre-treated, corrosion-resistant coatings frequently used on these screws further attest to their longevity, strengthening trust amongst users who require durable solutions in environments exposed to moisture or corrosive agents.
Furthermore, advancements in metallurgy and engineering have facilitated the development of self tapping wafer screws that can engage an increasingly broad spectrum of substrates. From thin aluminum sheets to plastics reinforced with carbon fiber, these screws provide a versatile option without the need to switch fastener types for different materials. Leading manufacturers continue to research and incorporate cutting-edge technologies, such as nanocoatings for enhanced corrosion resistance and optimized thread geometries for reduced installation torque. These innovations ensure that self tapping wafer screws not only keep pace with contemporary engineering demands but often lead the way.
These attributes collectively position self tapping wafer screws as a practical, efficient, and dependable choice across numerous applications. Engineers and manufacturers looking to streamline production without compromising quality find these screws to be an invaluable tool. Through continuous innovations and adherence to high standards, self tapping wafer screws are certain to remain an essential element in advancing modern construction and manufacturing methodologies. Embracing them in your projects assures a blend of simplicity and sophistication, supporting the growing complexities of contemporary engineering challenges.