When it comes to ensuring sturdy and reliable construction, shield anchors play a pivotal role. These dynamic fastening tools offer security in a variety of settings, whether in industrial setups, commercial buildings, or home improvement projects. But what exactly makes shield anchors indispensable, and how does one navigate their optimal use? Here’s a deep dive into the expertise required for handling this essential fastening solution.
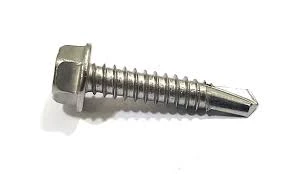
Shield anchors, also recognized as expansion anchors, are designed specifically to provide a permanent and reliable hold in materials such as concrete, brick, and block. These anchors work by expanding against the walls of the drilled hole, creating a tight grip that secures heavy loads. Their relevance surfaces in scenarios demanding top-notch safety and longevity, where typical fasteners might not suffice.
From an expert perspective, selecting the correct shield anchor involves understanding both the material of the walls you're working with and the weight of the object you intend to fasten. Not all projects should be treated equally. For example, light fixtures might require a different specification compared to industrial machinery mounts. Performance depends significantly on factors such as the depth of the hole, the diameter of the anchor, and the nature of the load.
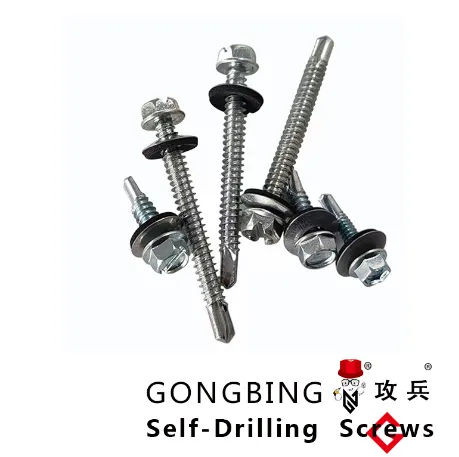
True expertise shines through in the installation process, where precision is paramount. The first step involves drilling a hole into the substrate that matches the diameter of the shield anchor. This requires special drill bits suited for hard materials. A common pitfall to avoid is making the hole too large; this would reduce the anchor's efficiency. Maintaining the recommended depth, usually outlined by the anchor manufacturer, is crucial to hold integrity.
One must trust established norms and manufacturers’ guidelines. Leading manufacturers usually test their products extensively, ensuring compliance with international safety standards. The credibility of documentation offered by established brands supplements their authority in the industry. Choosing products backed by a thorough testing process not only ensures peace of mind but also upholds safety regulations.
User experience often highlights the challenge of removing shield anchors once installed. Due to their robust holding power, extracting them can be difficult, hence the importance of correct initial installation to avoid unnecessary adjustments. The professional approach would be to maintain tools like an adjustable wrench and a hammer drill to manage the extraction should it be necessary.
shield anchors
A pertinent tip that comes from field experience is focusing on the long-term viability of the installed anchor. Variables such as exposure to harsh weather conditions, vibration, and chemical exposure should be considered and addressed with additional coatings or specific treatments that enhance the durability of the installation.
To instill trustworthiness, shield anchors options must be analyzed not just for immediate application, but also for extending to specialty uses such as seismic retrofitting and marine environments. Choosing the right material, galvanized or stainless steel, for instance, becomes a critical decision when facing corrosive environments.
In addition to the technical nuances, comprehending the economic aspect is also valuable. Initial investment in high-quality shield anchors might seem excessive, but their resilience often translates into reduced maintenance costs and longer service life. This practical wisdom supports the notion that in construction, opting for superior solutions is genuinely an investment.
Authoritativeness in the realm of shield anchors is recognized by aligning oneself with builders and industry organizations, sharing insights and validating techniques. Active participation in forums, workshops, and training sessions with other experts elevates one’s influence in the community.
In summary, using shield anchors effectively requires a calibrated blend of technical knowledge, practical experience, and an unwavering adherence to manufacturers’ advice and safety standards. This trifecta not only guarantees a robust, long-lasting assembly but fosters a reputation rooted in reliability and expertise.