Stainless steel self-threading screws have emerged as an essential component in modern construction and manufacturing industries, celebrated for their exceptional durability, corrosion resistance, and versatile application potential. Unlike traditional screws, these innovative fasteners have the unique ability to efficiently cut through material, forming their own threads during installation. This attribute not only simplifies the assembly process but also enhances the integrity and longevity of the structures they help create.
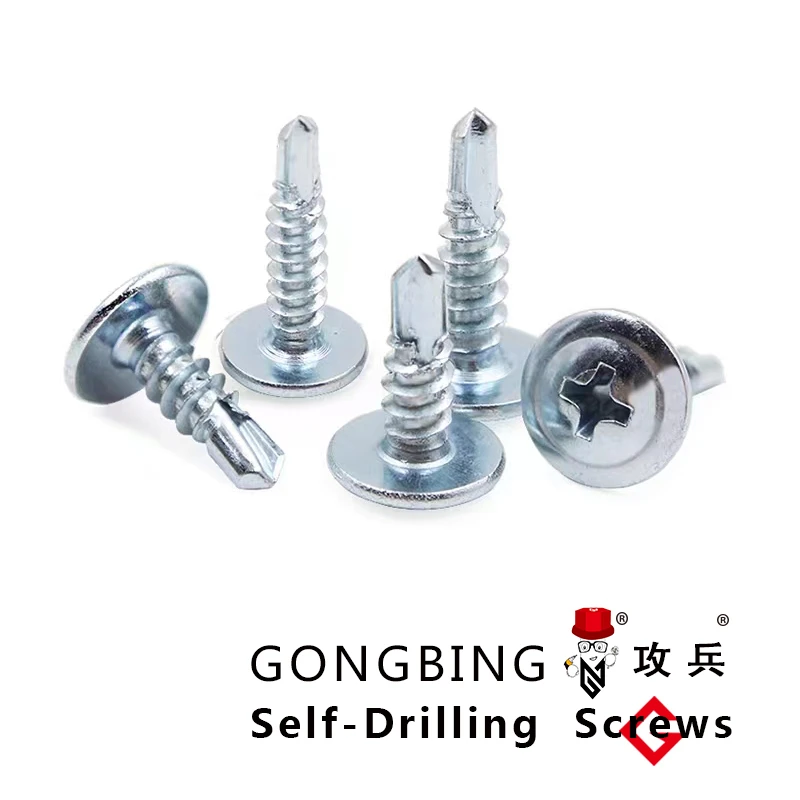
The first-hand account of using stainless steel self-threading screws reveals a significant transformation in the efficiency and reliability of assembly projects. Builders and contractors often highlight their ease of use, as these screws eliminate the need for pre-drilling, thus saving time and reducing labor costs. Their ability to self-tap into most substrates, including metals, wood, and plastics, underscores their adaptability across different tasks and environments. This is particularly beneficial in situations that demand strong, secure fastening without demanding extensive preparation work.
Expertise in the selection and application of stainless steel self-threading screws significantly contributes to successful outcomes in building projects. Professionals in engineering and construction emphasize the importance of understanding the grade and type of stainless steel used, as it directly affects the screw's performance. Grades such as 304 and 316 are commonly chosen for their excellent corrosion resistance, which is crucial in environments exposed to moisture and chemicals. Engineers and material scientists often advise careful consideration of the screw's design, such as its pitch, diameter, and thread pattern, to ensure optimal performance for specific applications.
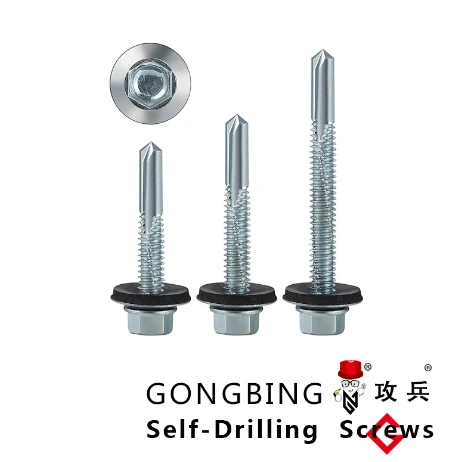
Authoritativeness in this domain is derived from a combination of scientific research, field studies, and substantial industry experience. Technical reports and scholarly articles often delve into the mechanical properties and failure modes of stainless steel self-threading screws, providing the empirical data needed to understand their behavior under diverse conditions. Workshops and industry conferences offer platforms for experts to share insights, discuss innovations, and develop best practices, further reinforcing the community’s collective knowledge and authority.
stainless steel self threading screws
Trustworthiness is pivotal when discussing the usage of stainless steel self-threading screws, especially in safety-critical applications such as structural framing or securing components in machinery. Manufacturers earn trust by adhering to stringent quality control measures and international standards like ISO or ASTM, ensuring that the screws meet rigorous mechanical and chemical specifications. Product certifications and audit reports add an additional layer of confidence for buyers and users, verifying that the screws have been tested for reliability and performance.
In the realm of product selection, buyers are encouraged to assess not only the mechanical properties but also the environmental impact and sustainability of the screws. Stainless steel is inherently a more sustainable choice due to its recyclability and long service life, compared to other materials that may require frequent replacement and produce more waste. Ethical sourcing and production practices further enhance the appeal of choosing stainless steel self-threading screws as a responsible and environmentally sound option.
Ultimately, the successful application of stainless steel self-threading screws hinges on an informed approach that balances technical requirements with practical considerations. Whether for commercial, residential, or industrial use, these screws offer a reliable solution that combines ease of installation with superior performance characteristics. Their adaptability across a broad range of applications not only underscores their importance in modern construction but also highlights the continued evolution and innovation within fastening technology.