Structural fasteners are a fundamental component in the construction and engineering industries, crucial for ensuring stability and safety in various applications. With the rapid evolution of construction technologies, understanding the nuances of structural fasteners has become ever more important for engineers, builders, and safety inspectors. These small components carry a vast weight of responsibility, holding together the frameworks of buildings, bridges, and other critical structures.
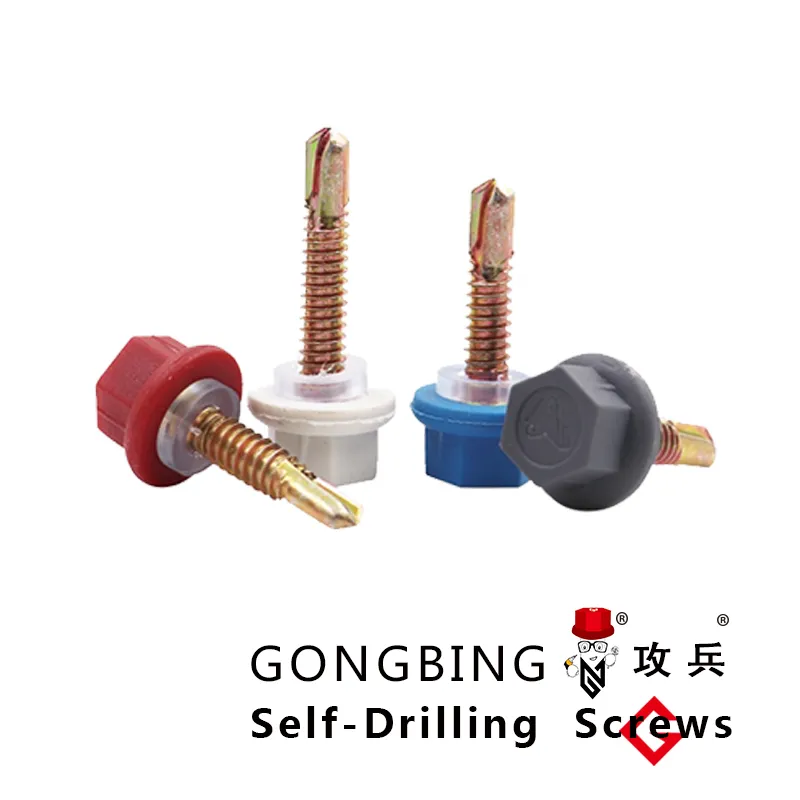
Experience plays a pivotal role in selecting and applying structural fasteners effectively. Industry veterans know that the right fastener can make the difference between structural integrity and catastrophic failure. These experienced professionals understand that choosing the appropriate fastener involves more than just matching sizes. It's about recognizing load requirements, environmental factors, and material compatibilities. For instance, in coastal regions where saltwater exposure is a concern, stainless steel or galvanized fasteners are preferred to prevent corrosion, ensuring longevity and durability.
When delving into expertise, understanding the various types of structural fasteners is critical. Common types include bolts, screws, anchors, nuts, and washers, each serving unique purposes. Bolts and screws are used when components need to be clamped together securely, whereas anchors are essential for attaching elements to concrete or masonry. Expert knowledge is required to determine not only the type but also the grade and material of the fastener. For example, high-strength bolts (often made from alloyed steel) are necessary in situations where extreme forces are at play, such as in the construction of skyscrapers or large-span bridges.
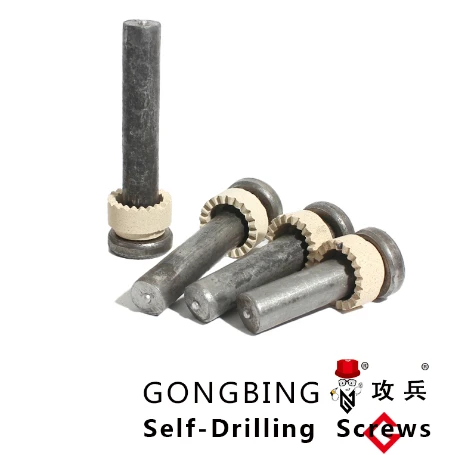
Authoritativeness in the realm of structural fasteners comes from thorough compliance with international standards and guidelines. Organizations such as ASTM International, the American Society of Mechanical Engineers (ASME), and the International Organization for Standardization (ISO) provide exhaustive standards that dictate material compositions, dimensions, and performance characteristics. Adhering to these standards not only ensures the quality and safety of the fasteners but also reinforces a commitment to industry best practices. Companies that demonstrate a strong adherence to these guidelines are often seen as leaders in the field, providing products that professionals can trust.
Trustworthiness is another significant aspect, particularly when it comes to manufacturers and suppliers of structural fasteners. Reliability in sourcing these critical components stems from consistent quality, traceability, and transparency in manufacturing processes. Reputable manufacturers provide comprehensive technical data sheets and testing certifications for their products, enabling engineers and builders to make informed decisions. Additionally, third-party audits and quality assurance tests further establish trust, ensuring that the fasteners will perform as expected under specified conditions.
structural fasteners
Shifting to product specialization, advancements in structural fastener technology are continually improving the construction landscape. Innovative designs, like self-tapping screws or expansion anchors, have simplified installation processes and increased efficiency in various applications. Self-tapping screws, for instance, help reduce labor time by cutting their own threads into softer materials. Expansion anchors, by design, create a secure hold within concrete or brickwork, proving invaluable in seismic areas where added stability is crucial.
The burgeoning field of smart fasteners is another exciting development, merging traditional fastener applications with modern technology. These are equipped with sensors that monitor strain, temperature, and other environmental factors, sending data to centralized systems for analysis. By providing real-time monitoring, smart structural fasteners present new opportunities for preventative maintenance and structural health monitoring, allowing for proactive measures to avoid failures and extend the lifespan of structures.
The importance of proper structural fastener selection and application cannot be overstated. With the growing complexity of modern architecture and engineering, ensuring these small, often overlooked components are chosen and installed correctly is crucial for safety and performance. By integrating experience, expertise, authoritativeness, and trustworthiness into every aspect of their selection and use, industry professionals can uphold the highest standards of construction and engineering.
As technology continues to evolve, the demand for more advanced fasteners will grow, pushing the boundaries of what these components can achieve. Staying abreast of the latest advancements and maintaining a commitment to quality and safety will ensure that structural fasteners continue to play their pivotal role in building a safe and resilient future.