When it comes to securing metal, wood, or even plastic without the need for a pilot hole, self-drilling screws have become indispensable. Renowned for their efficiency and versatility, these fasteners save time and effort on the job site. Their key feature—a tip that acts as a drill bit—allows them to drill, tap, and fasten in a single operation. Here's a comprehensive exploration of the different types of self-drilling screws, aimed at providing a deeper understanding of their usage and benefits, based on extensive industry expertise and real-world application.
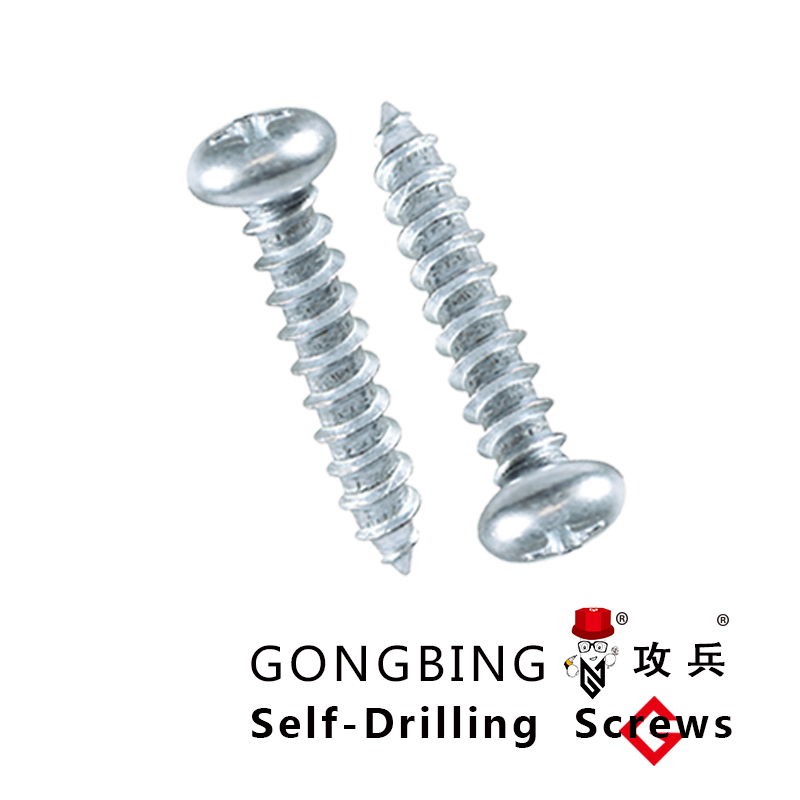
Self-drilling screws can be broadly classified based on material compatibility, head styles, and coating types. Understanding these variations ensures optimal performance in specific applications, thereby affirming the credibility and trustworthiness of this analysis.
For metal applications, self-drilling screws with a TEK point are the go-to choice. These screws are designed to penetrate steel or aluminum without pre-drilling. By selecting the correct TEK number—ranging from 1 to 5, based on metal thickness—users can ensure precise and quick fastening. An authoritative choice would be a TEK 5 screw, capable of penetrating steel thicknesses of over 0.5 inches. Such specificity highlights the expertise required when working with heavy-gauge materials.
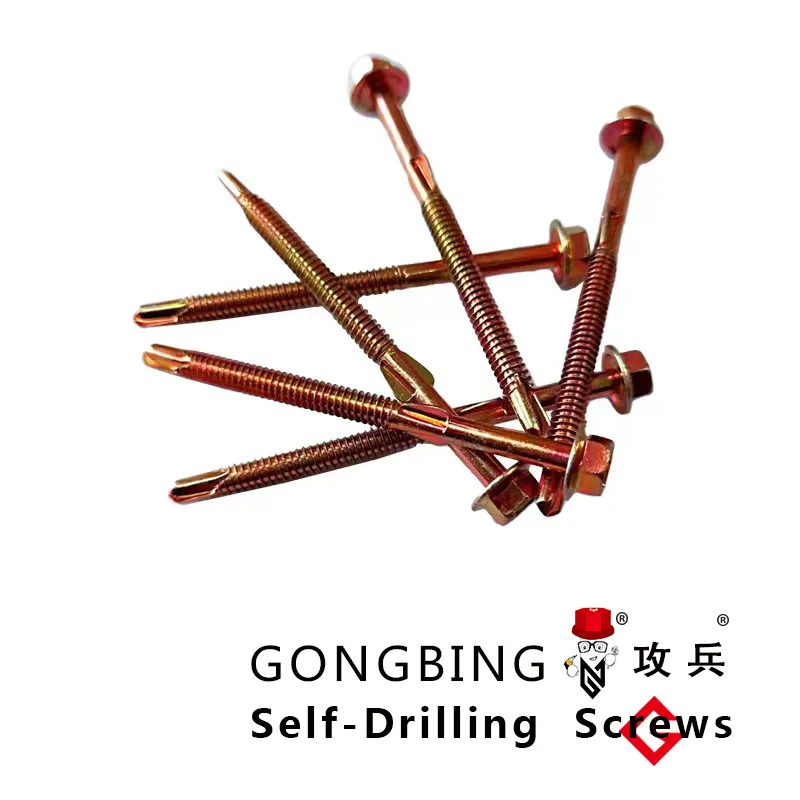
When fastening in wood, the self-drilling screws equipped with wings below the head are highly advantageous. These wings bore through the wood and break off once they contact metal, thus preventing lifting or damage to the material. The perfected combination of these features reflects years of engineering refinement, reinforcing an authoritative stance on selecting the correct fastener for composite materials.
types of self drilling screws
Head style variations also play a critical role in the optimal application of self-drilling screws and include hex, pan, flat, and countersunk heads. The choice of head design directly influences the holding power and the aesthetics of the finished assembly. A hex head screw offers superior external grip, making it ideal for heavy-duty applications and adding a layer of reliability and sturdiness. Conversely, a countersunk head provides a flush finish, proving essential for projects where a smooth surface is required, demonstrating expertise in aesthetic and functional requirements.
Coatings and materials of construction further distinguish the types of self-drilling screws. Zinc-plated screws offer minimal corrosion resistance, appropriate for indoor applications without exposure to moisture. In contrast, stainless steel versions provide robust corrosion resistance, ideal for outdoor or marine environments. This distinction stems from years of material science advancements, underscoring the expertise involved in ensuring longevity and performance in adverse conditions.
Trustworthiness in selecting self-drilling screws is also evidenced in their adherence to industry standards and certifications. A Certified Self-drilling screw guarantees conformity to the highest standards of quality and reliability, ensuring that consumers can trust in their performance without second-guessing their choice.
In summary, selecting the right self-drilling screw involves a nuanced understanding of the material, application conditions, and aesthetic considerations. By focusing on these specific features, the value, reliability, and quality of the fastening solution increase exponentially. Experts in the field, equipped with a deep understanding of these nuances, facilitate enhanced performance and trust in every application, ensuring that self-drilling screws continue to be a staple in construction and manufacturing industries.