Tek screws, often referred to as self-drilling screws, are a fundamental component in the construction and manufacturing industries. Known for their unique ability to drill their own pilot holes as they are driven into materials, these fasteners offer efficiency and reliability when joining metal to metal or even metal to wood. Understanding the various types of tek screws can vastly improve the efficacy of any project.
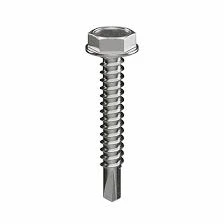
The most common types of tek screws are categorized primarily by their head, drive, and tip style, each serving specific functions. Starting with head styles, hex head tek screws are widely preferred in projects requiring higher torque and are frequently employed in metal roofing. The large, hexagonal head provides substantial surface area, facilitating a secure grip—even with power tools. Conversely, pan head tek screws are used where a flat, finished appearance is desired, often in visible applications where aesthetics are important.
Drive styles are another essential consideration, impacting how the screw is inserted. Tek screws predominantly feature Phillips, square, or Torx drives. Phillips drives are ubiquitous due to their cross-slot design, which helps to center the screw and reduce slippage during installation. Meanwhile, square drives, also known as Robertson drives, offer reduced cam-out, providing a more stable driving experience by nesting the bit snugly into the screw head. Torx drives, with their star-shaped pattern, deliver superior torque transfer and are particularly useful in industrial applications where repeated installation and removal may occur.
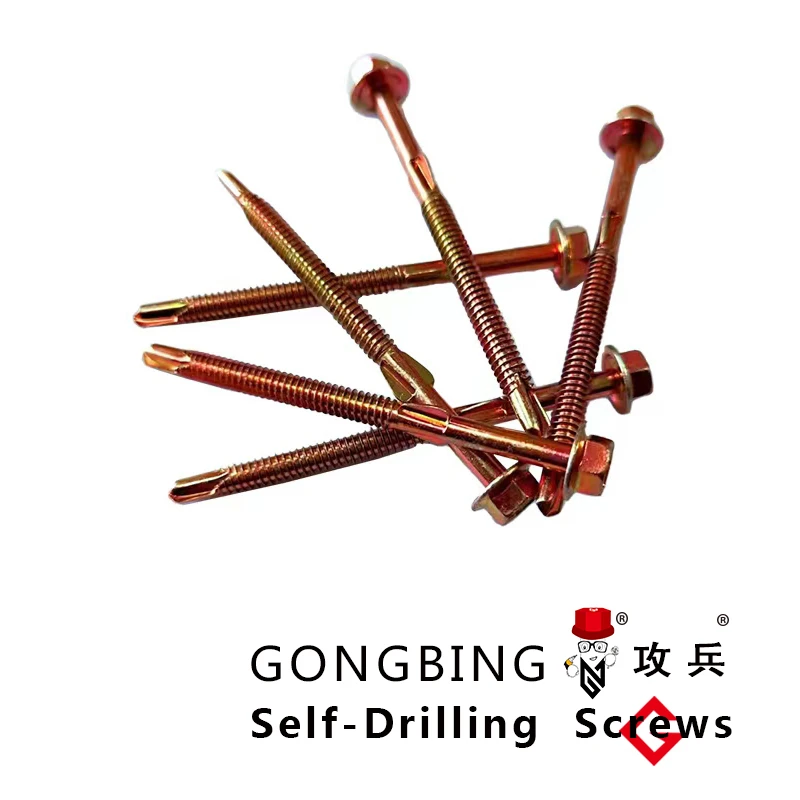
The tip of a tek screw is arguably its most critical aspect. These screws boast self-drilling capabilities thanks to their specially engineered tips, eliminating the need for pre-drilled pilot holes. The most standard types are numbered 2, 3, and 5, each indicating the screw’s drilling capacity in terms of metal thickness. A 2 tek screw, for example, is apt for thinner metals, whereas a 5 can penetrate thicker gauge materials. This ability to pierce through metal efficiently reduces construction time and labor costs, optimizing workflow in demanding assemblies.
types of tek screws
Material composition further diversifies the types of tek screws. While carbon steel is commonly used due to its affordability and durability, stainless steel tek screws offer superior resistance to rust and corrosion, making them ideal for outdoor applications or environments exposed to moisture. Zinc-plated alternatives provide an additional level of corrosion resistance without the expense of stainless steel.
Tek screws also come with varied thread styles, specifically fine and coarse threads. Fine threads deliver greater holding power in metal, perfect for security in high-stress applications. Coarse threads are preferable for quicker installation though they may sacrifice some holding strength.
Choosing the right type of tek screw can influence not only the success of a project but also its efficiency and longevity. Professionals typically assess the project's requirements, such as material type and thickness, environmental exposure, and aesthetic demands, to select the best-suited screw.
In conclusion, understanding the diverse array of tek screws—from head and drive styles to tip designs and material compositions—reveals the importance of selecting the right fastener for the job. Experienced professionals count on tek screws for their self-sufficiency and strength, ensuring that structures are built to last while maintaining precision and efficiency throughout the process. Whether in residential construction, industrial fabrication, or metalworking, the correct choice of tek screw can significantly affect project outcomes, emphasizing the principle that quality fastening solutions underpin successful assemblies.