In the world of construction and renovation, precision and reliability are paramount. Chemical anchors, often overlooked by the uninitiated, have emerged as essential tools for securing materials where traditional methods might fall short. These anchors, offering a blend of strength and versatility, are being increasingly adopted across diverse applications. This article seeks to delve into the particulars of chemical anchors, highlighting their advantages, applications, and the intricacies involved in their deployment.
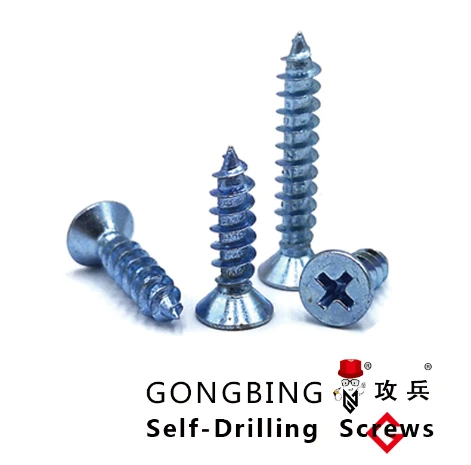
Chemical anchors, also known as bonded anchors, utilize a resin-based adhesive that fortifies the connection between a fixture and a substrate such as concrete, stone, or other materials. The technology behind chemical anchoring has continually evolved, and today, it represents a significant leap beyond mechanical fastening methods, especially when addressing the challenges posed by dynamic loads or edge proximity issues.
The strength of chemical anchors is one of their most compelling attributes. Unlike mechanical anchors that rely on the stress and friction between the materials, chemical anchors create a more uniform distribution of stress across the bonded surfaces. This characteristic is particularly beneficial in structural applications where high tension and shear loads are expected. Moreover, the curing process of the resin—when combined with the optimal design of the anchor—can offer unparalleled pull-out resistance, thus enhancing the safety and durability of the construction.
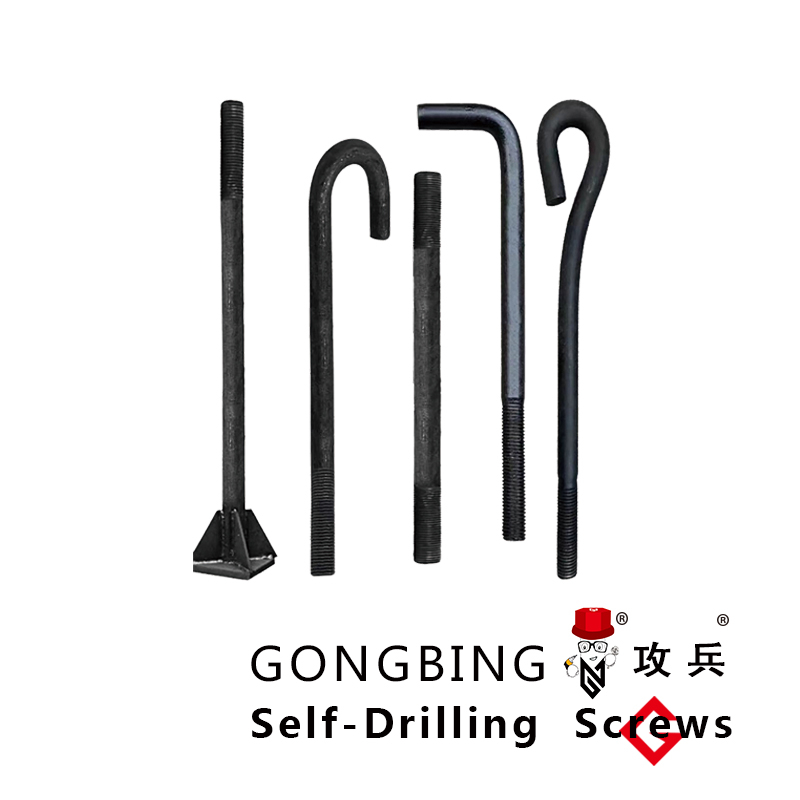
From bridges and high-rise buildings to industrial equipment and even home renovations, the areas where chemical anchors prove useful are extensive. In bridge construction, for example, the ability to sustain significant loads and the flexibility to adapt to different environmental conditions underscore the value of chemical anchors. Similarly, in the mounting of heavy machinery, where vibrations are a constant factor, the reliability of chemical anchors can ensure equipment stability, thereby mitigating risks of operational failure.
The expertise required to effectively use chemical anchors should not be underestimated. Proper installation is crucial to harnessing their full potential. This begins with choosing the appropriate type of resin—epoxy, polyester, or vinylester—each offering distinct properties suited for different environmental conditions and load requirements. For instance, epoxy-based resins are particularly advantageous in wet conditions and can often be used with confidence in cold weather settings due to their superior moisture resistance and bond strength.
using chemical anchors
Correct hole preparation is another critical aspect of their effective use. The precise drilling of holes, accurate cleaning to remove debris, and ensuring the right diameter and depth can significantly impact the anchor's performance. Any residue in the drilled hole can impede the bond of the resin with the substrate and the anchor rod, thereby compromising the system's overall efficacy.
Another cornerstone of chemical anchoring is the curing process. Curing time can vary based on environmental conditions, the type of resin used, and the ambient temperature. Installers must have detailed knowledge and follow manufacturer specifications to ensure that the anchor achieves the desired strength. Premature loading of the anchor before full curing can lead to failures, emphasizing the need for patience and adherence to guidelines during the entire process.
The authority of chemical anchors in the construction toolkit is reinforced by their certifications and compliance with international standards such as the European Technical Assessment (ETA) and American Concrete Institute (ACI) guidelines. These certifications guarantee that the products meet rigorous safety and performance criteria, fostering trust among engineers and builders who rely on these products for critical applications.
Trustworthiness in chemical anchors also comes from reputable manufacturers who invest in research and development to advance the technology. Companies that lead in innovation not only deliver high-quality products but also provide comprehensive support and education to ensure that their products are installed safely and effectively. This role of manufacturers in disseminating knowledge cannot be overstated, as it bridges the gap between product development and end-user implementation.
In conclusion, the application of chemical anchors is not just a matter of selecting the right product but also of handling it with the finesse that comes from understanding both the material science and the practical challenges of the construction environment. As their use continues to grow, the industry can anticipate even more sophisticated solutions emerging, enabling safer and more resilient constructions worldwide. By staying informed about technological advancements and best practices, engineers and construction professionals can deploy these anchors with confidence, ensuring the integrity and longevity of their projects.