The Art of Precision in Wafer Head Metal Screws
In the intricate world of manufacturing, few components epitomize precision and functionality as succinctly as wafer head metal screws. These humble fasteners are the unsung heroes of numerous industries, from electronics to aerospace, where their unique design and material properties contribute to the seamless operation of complex systems.
The wafer head, characterized by its flat, circular head that sits flush with the surface it secures, is a testament to minimalism in industrial design. Unlike the traditional Phillips or slotted screws, the wafer head's profile offers a sleek appearance, reducing both wind resistance and the risk of snagging. This feature is particularly crucial in applications where aesthetics or aerodynamics play a vital role.
Made from various metals such as stainless steel, brass, or titanium, these screws boast exceptional strength and corrosion resistance. The choice of material often depends on the application's demands; for instance, stainless steel is preferred in environments exposed to moisture, while titanium is utilized in weight-critical aerospace projects.
The manufacture of wafer head metal screws is an art form that requires precise machinery and skilled operators. The process begins with selecting high-quality metal stock, which is then cold-formed into wires of consistent diameter. These wires undergo a heading process where the distinctive wafer shape is formed. Each screw is then threaded meticulously to ensure a tight, secure fit every time it's used.
One notable advantage of wafer head screws is their drive recess, typically designed for an Allen wrench or a Torx driver
One notable advantage of wafer head screws is their drive recess, typically designed for an Allen wrench or a Torx driver
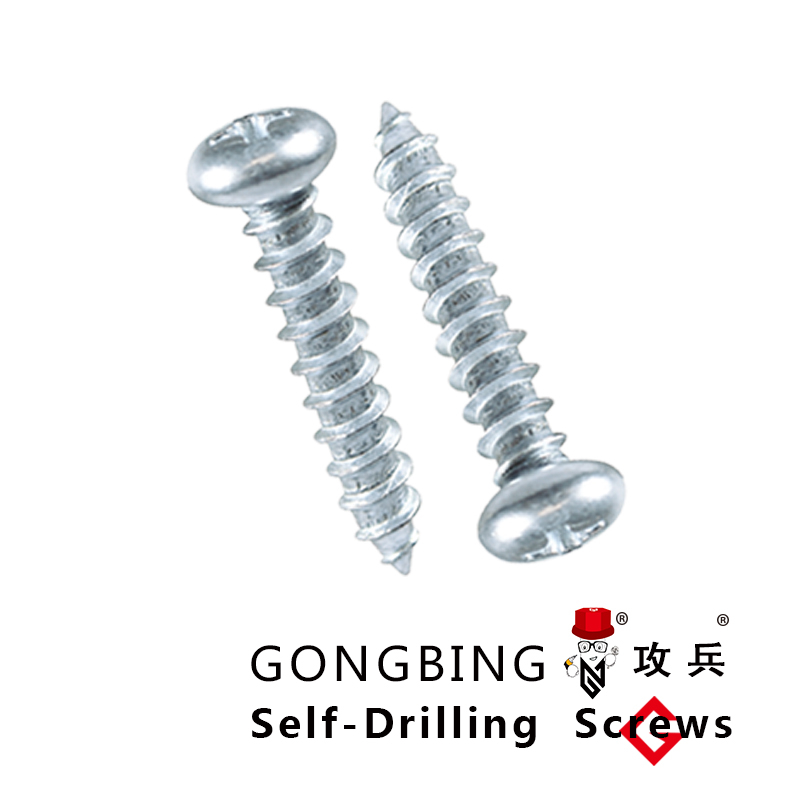
One notable advantage of wafer head screws is their drive recess, typically designed for an Allen wrench or a Torx driver
One notable advantage of wafer head screws is their drive recess, typically designed for an Allen wrench or a Torx driver
wafer head metal screws. This recess is deeper and more defined than in other screw types, allowing for better tool grip and reducing the risk of stripping. It also enables the application of higher torque, making them ideal for heavy-duty tasks.
In terms of application, wafer head metal screws shine in environments where adjustments are frequent. Their low profile allows tools to easily access and manipulate them, simplifying maintenance and repair work. In electronic enclosures, they provide a clean look while ensuring that panels are securely attached. Similarly, in automotive interiors, they hold components together without detracting from the vehicle's aesthetic appeal.
The next time you encounter a wafer head metal screw, consider the journey it has undertaken – from raw material selection to precision manufacturing. Each screw embodies engineering excellence, a silent partner in the grand machinery of our modern world. They may be small, but their contribution to the function and form of countless devices is immeasurable.