Self-drilling screws are a vital component in construction and metalworking, offering efficiency and reliability that traditional fastening methods can’t match. With their innovative design, these screws eliminate the need for pre-drilling, making them indispensable for both professionals and DIY enthusiasts. This article focuses on understanding the unique benefits, applications, and selection criteria associated with self-drilling screws, ensuring an authoritative guide to choosing the right screws for your project.
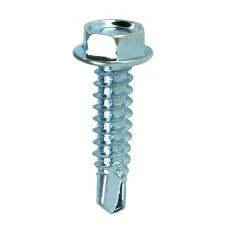
The evolution of self-drilling screws has revolutionized the way materials, particularly metals, are fastened together. By integrating a drill point into the screw itself, they streamline the fastening process, significantly reducing assembly time and labor costs. Their ability to penetrate metal surfaces without a pilot hole makes them ideal for applications in roofing, facades, and general construction, where speed and durability are paramount.
In the world of construction, efficiency is king, and self-drilling screws reign supreme by offering a solution that minimizes the steps involved in securing materials. The screws' design features a helical thread and a drill point, which work in unison to cut and secure the material simultaneously. This design not only saves time but also reduces the risk of material damage associated with traditional drilling and fastening methods.
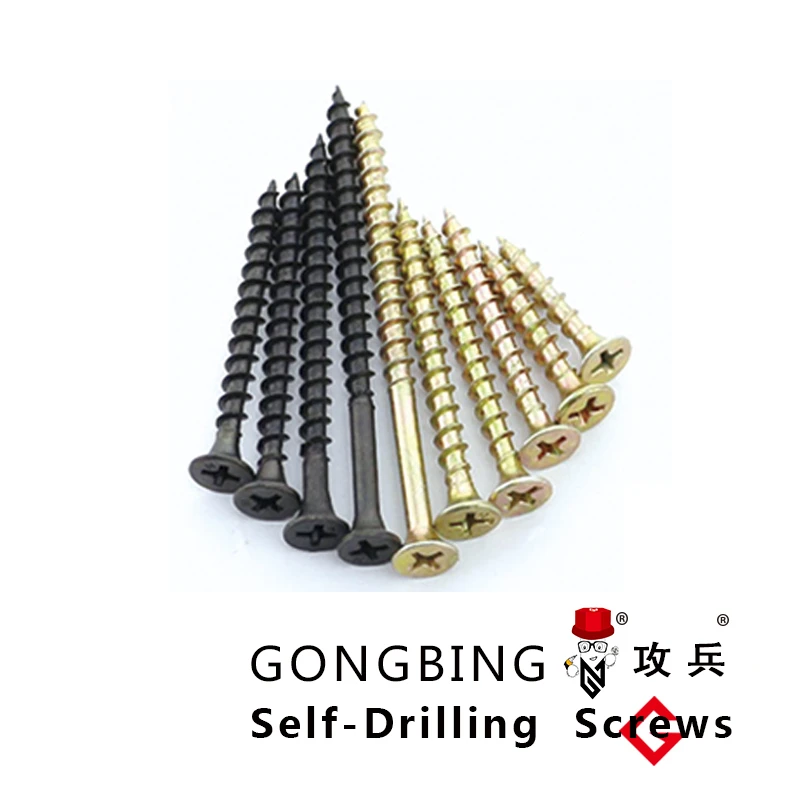
A practical example of their expertise can be seen in the roofing industry, where self-drilling screws are regularly used to attach metal sheets to structural frames. Roofing applications demand fasteners that can withstand environmental stressors, such as wind, rain, and thermal expansion. The robustness of self-drilling screws ensures a tight and secure fit that maintains structural integrity under these conditions.
Moreover, self-drilling screws come in various point designs and lengths to accommodate different material thicknesses and types, enhancing their versatility. Understanding the specifics of your project, like material composition and environmental exposure, is crucial when selecting the correct screw type. This requires an understanding of technical specifications, such as point type (e.g., TEK 3 or TEK 5), thread density, and coating materials that resist corrosion.
4 self drilling screws
Experts recommend considering the self-drilling screw’s coating, such as zinc or galvanization, to prevent rust and degradation when exposed to harsh environmental conditions. A coated screw not only extends the life of the fastening but also ensures a clean, aesthetically pleasing appearance, especially in visible applications.
From a professionalism standpoint, the authoritative use of self-drilling screws also lies in adhering to industry standards and regulations, which dictate the performance and safety of fastening systems. Professionals should consult guidelines from organizations such as the American Society for Testing and Materials (ASTM) to meet these standards.
Trustworthiness in the use of self-drilling screws is demonstrated through proper installation techniques. This involves using compatible tools and applying the correct torque to avoid over-tightening, which can strip threads or damage materials. Installation best practices ensure the fasteners perform as expected, maintaining the longevity and reliability of the structure.
In summary, the world of self-drilling screws is complex, yet understanding their application offers significant benefits in terms of time, cost, and structural integrity. They stand as a testament to modern engineering, reflecting the expertise and innovation integral to contemporary construction. When chosen and installed correctly, self-drilling screws don’t just hold materials together—they hold the future of fast construction solutions in their threads.