Understanding the diverse types of self-drilling screws is essential for anyone involved in construction, manufacturing, or any DIY projects. These screws, renowned for their efficiency in cutting through metal sheets without pre-drilling, are indispensable. Navigating the varied types can dramatically enhance the outcome of structural integrity and efficiency.
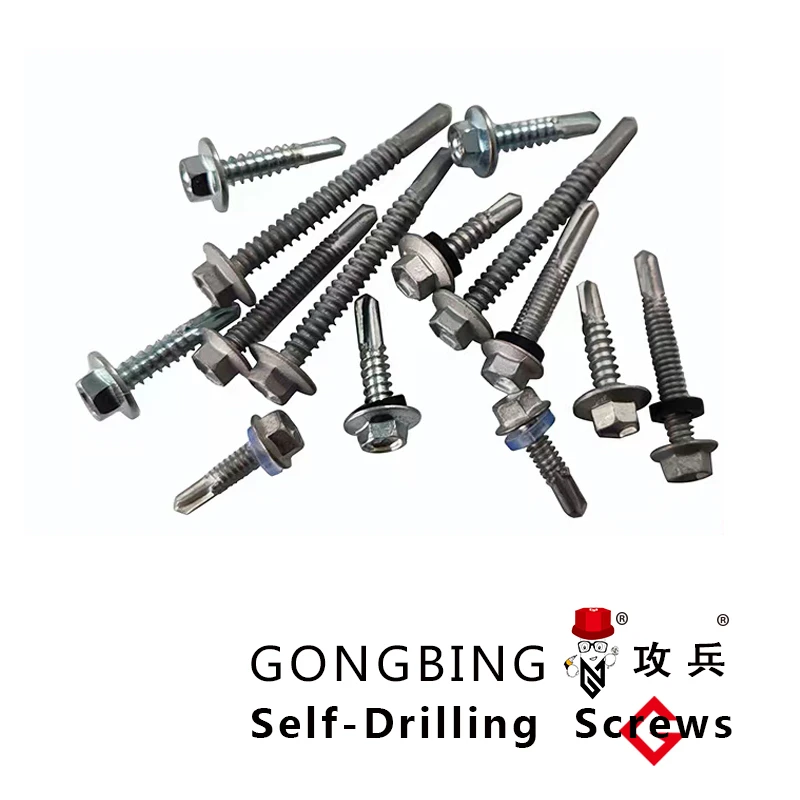
Self-drilling screws, tailored uniquely for metal-to-metal or metal-to-wood applications, come in several forms, each optimized for distinct tasks. Starting with the head design, the Phillips head and the hex washer head are common. The Phillips head self-drilling screw, characterized by its distinctive cross-shaped recess, offers a versatile fit for most applications. It is highly favored in applications requiring a flush finish due to its flat-head design, seamlessly integrating into the surface.
Meanwhile, the hex washer head is designed for applications demanding higher torque. The robustness provided by the hexagonal head design allows for greater force application without slippage, making it an ideal choice for industrial uses where precision and strength are critical. Paired with a rubber washer, it provides a watertight seal, crucial for outdoor assemblies exposed to the elements.
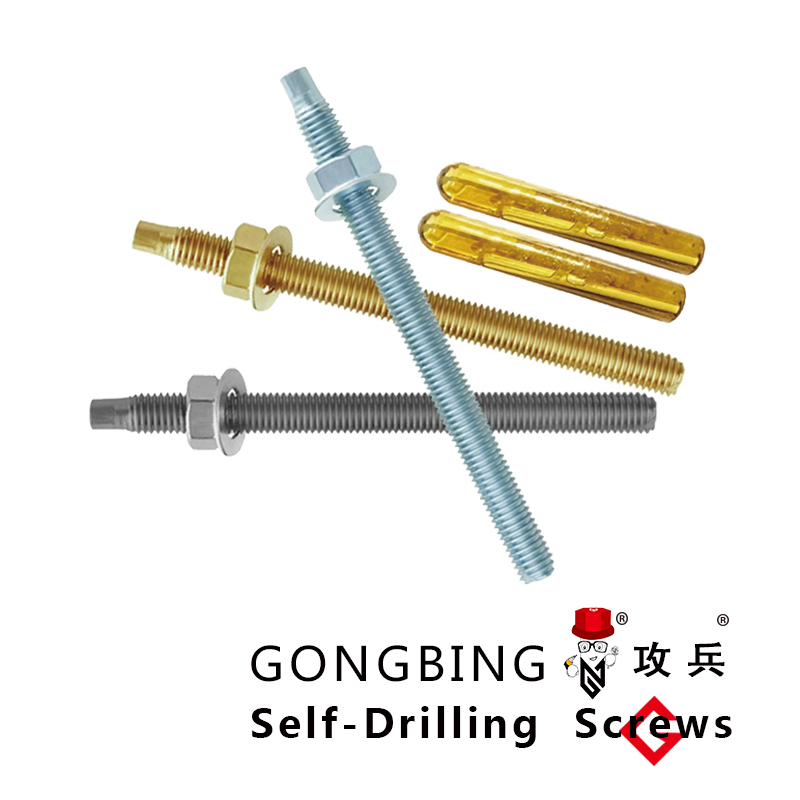
Distinguishing self-drilling screws through their point designs is also pivotal. The standard point—a classic choice for lightweight metal—is engineered meticulously for precision drilling, ensuring optimal grip with minimal walking on the material surface. This design is particularly beneficial for thin sheet metal, offering the needed penetration without damaging the material.
For applications involving thicker materials, self-drilling screws with a winged tip design excel. These wings enlarge the hole in wood materials, preventing thread engagement, allowing the screw to reach the metal layer before snapping off. This innovation guarantees a smoother transition and a tighter fit, ensuring enhanced structural stability.
types of self drilling screws
Further, stainless steel self-drilling screws are highly esteemed for their corrosion resistance, an essential quality in maritime, automotive, and coastal projects. Coupled with self-drilling capabilities, these screws promise longevity and reliability, reducing the need for frequent replacements and maintenance in harsh environments.
The drill flute design plays a vital role in the performance of self-drilling screws. A well-designed flute enables efficient debris removal during drilling, reducing heat accumulation and enhancing the lifespan of the screw. Correct flute dimensions also facilitate smoother insertion while ensuring firm material adherence.
Selecting the correct self-drilling screw is pivotal to project success. Precision in choice ensures secure fastening, prevents material damage, and enhances load-bearing ability. It is advisable to consider the material thickness, environmental conditions, and force requirements to determine the ideal screw type for your application.
In conclusion, understanding the nuances of self-drilling screws transforms a simple fastening task into a well-executed project. Knowledge and expertise in selecting the right type promise efficiency and durability, essential attributes for any project poised for success. As the industry continually innovates, staying informed on the latest screw technologies is imperative for meeting evolving demands and maintaining high standards of workmanship.