The demand for self-drilling screws for thick steel surfaces calls for products that deliver exceptional performance, reliability, and durability. These screws play a pivotal role in construction, manufacturing, and industrial applications, offering unique advantages tailored to meet the strict requirements of thick steel connections.

When working with thick steel, the primary challenge is ensuring a secure and efficient fastening without the need for pre-drilling holes. Self-drilling screws, designed with a specialized drill bit point, streamline construction and assembly projects by negating this labor-intensive step. As a result, they save both time and resources while minimizing the risk of material damage or misalignment.
In terms of expertise, the choice of material and finish for self-drilling screws is crucial. High-quality screws are typically manufactured from case-hardened steel, which provides the necessary strength to penetrate thick steel surfaces. The hardiness of these screws ensures their ability to withstand immense pressure and torque during application, preventing snapping or bending.
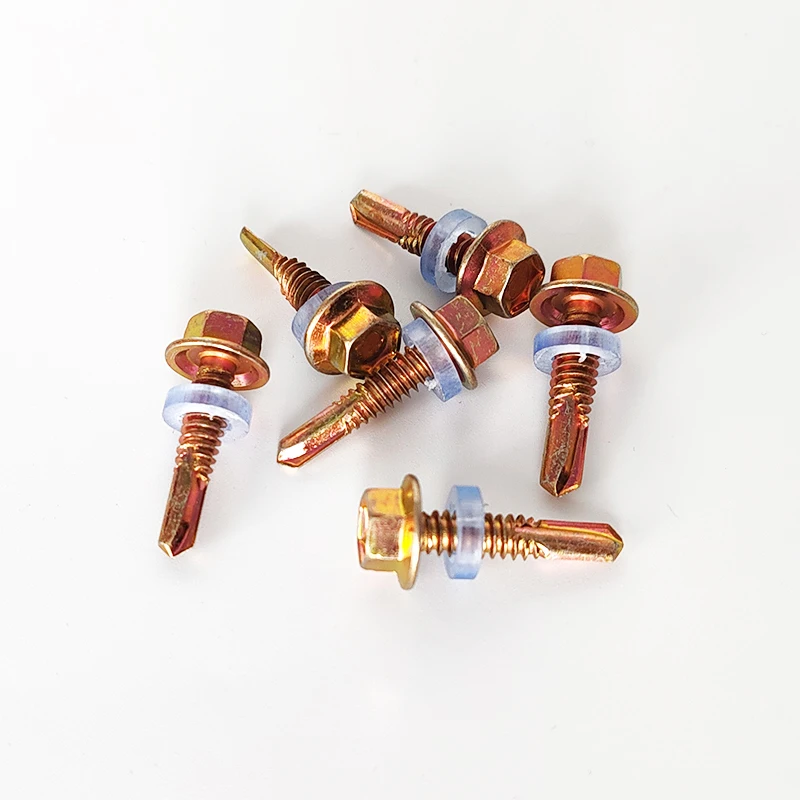
Additionally, considering factors such as coatings and plating is essential for enhanced performance and longevity. Zinc plating, for instance, provides excellent corrosion resistance, maintaining the integrity of the screw and the steel surface in various environmental conditions. Some manufacturers may also offer screws with specialized polymer coatings to further enhance resistance against wear and tear, chemical exposure, and weathering, making them ideal for outdoor or heavy-duty applications.
From an experiential standpoint, using self-drilling screws on thick steel requires understanding the nuances of screw selection and application. The size and thread design should correspond to the thickness and type of steel to ensure optimal grip and holding power. For instance, larger diameters with coarse threads may be preferable for heavier steel profiles, as they provide a better anchorage and distribute load effectively.
self drilling screws for thick steel
Proper installation techniques also enhance performance outcomes. When employing self-drilling screws, maintaining a consistent, perpendicular insertion angle can prevent misalignment and ensure maximum thread engagement. Using high-quality, power-driven impact drivers or screw guns, calibrated to suitable speed and torque settings, enhances the precision and efficiency of installation.
The credibility and authoritativeness of manufacturers offering these screws are equally important. Reputable brands provide detailed specifications and technical support, ensuring that their products meet industry standards and regulations. They often conduct rigorous testing to validate the performance and durability of their screws under varied conditions, lending confidence to the reliability of their claims.
Trustworthiness is further reinforced by customer testimonials and reviews that highlight real-world applications where these screws have excelled. Insights from professionals who have successfully utilized these screws in projects involving thick steel add valuable context, verifying product claims through documented successes and satisfied end-users.
In conclusion, selecting the right self-drilling screws for thick steel is a strategic decision that affects the quality and safety of construction and industrial projects. High-performance screws combine robust materials, thoughtful design, and rigorous testing, supported by trusted manufacturers with proven expertise in the field. Whether elevating the efficiency of construction projects or enhancing the durability of built structures, self-drilling screws for thick steel stand as a testament to innovation, precision, and reliability.