Countersunk chipboard screws are a vital component for both DIY enthusiasts and construction professionals, providing an effective solution for fastening chipboard and other composite materials. With years of experience and expertise, understanding the nuances of these screws can significantly improve project outcomes.
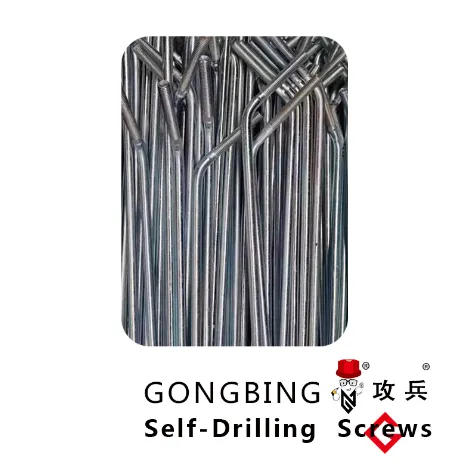
When considering countersunk chipboard screws, one key aspect is their design. Their conical-shaped heads allow them to sit flush with or below the surface of the material. This feature is crucial for applications where aesthetics and a smooth finish are important. An expert would advise choosing screws with threading that extends along the whole length. This maximizes grip and prevents any potential movement, ensuring the structural integrity of the furniture or fixture being assembled.
The choice of material and coating for these screws is equally important. High-quality countersunk chipboard screws are often made from hardened steel, which offers exceptional durability and strength, crucial for high-load applications. The screws are typically coated with corrosion-resistant materials like zinc or yellow passivation. This is a critical consideration for projects exposed to moisture or where longevity is a requirement. A seasoned professional would always emphasize not compromising on the rust-resistant properties of these screws, as it directly impacts the longevity and reliability of the assembly.
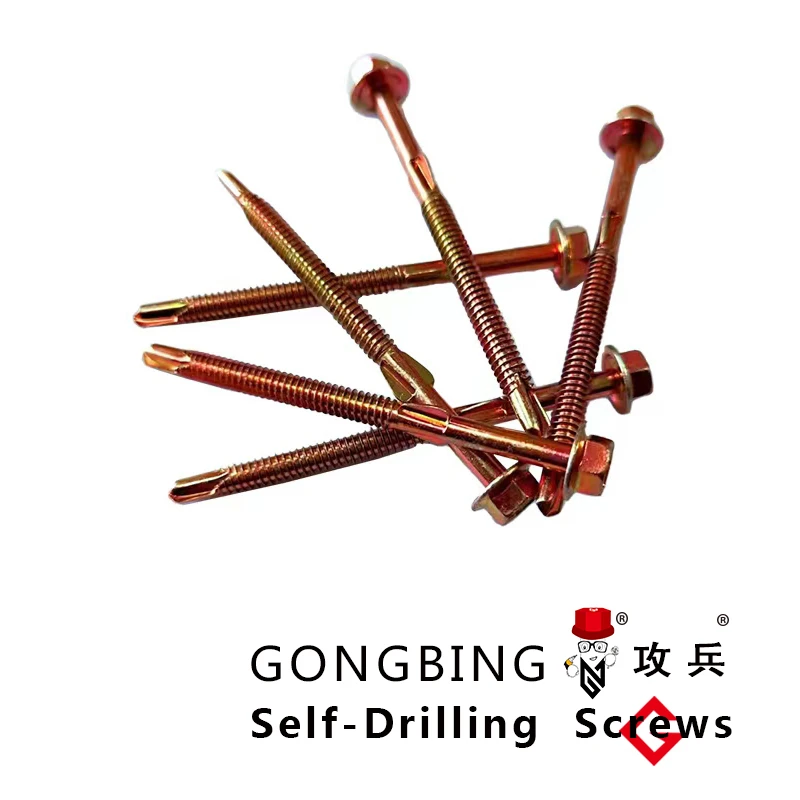
Installation techniques also play a vital role in maximizing the performance of countersunk chipboard screws. The use of an electric screwdriver with adjustable torque settings is recommended to avoid over-tightening, which can strip the material and compromise the fastening strength. Experts suggest pre-drilling pilot holes slightly smaller than the screw diameter in denser materials. This reduces the risk of splitting, ensuring the chipboard maintains its integrity and the screws securely fasten the components in place.
countersunk chipboard screws
From a safety standpoint, selecting the appropriate length and gauge of the screw is non-negotiable. This requires precision in measuring the thickness of the materials being joined to ensure the screw threads properly anchor without protruding from the opposite side. Trustworthiness comes from an understanding of your project's specific requirements and selecting the right screw specifications tailored to those needs. A trusted specialist in chipboard construction will always verify the compatibility between the screws and the material thickness prior to installation.
Moreover, for professionals seeking to enhance productivity and output quality, investing in countersunk chipboard screws of consistent quality and specification is advisable. This ensures every piece replicates the finish and strength characteristics of the last, which is particularly significant in manufacturing environments where uniformity is key. Using screws from a reputable manufacturer mitigates the risk of defects that could lead to structural weaknesses, saving time and cost related to rework or recalls.
Furthermore, creating a strong foundation with industry insights from reputable sources solidifies one’s authoritative voice in the field. Engaging with technical workshops, forums, and training programs can elevate one’s understanding of advanced fixing techniques and cutting-edge developments in screw technology. This knowledge not only benefits the individual projects but also positions one as a knowledgeable and reliable consultant in the eyes of clients or project collaborators.
In conclusion, investing time and effort into understanding and selecting the appropriate countersunk chipboard screws is fundamental to the success of construction projects involving composite materials. By focusing on design, material quality, proper installation techniques, and continuous learning, professionals and hobbyists alike can achieve optimal functional and aesthetic outcomes. These practices ensure that assemblies remain robust, reliable, and aligned with the highest standards of craftsmanship and durability.